Why plastic extrusion is ideal for mass production
Why plastic extrusion is ideal for mass production
Blog Article
Understanding the Fundamentals and Applications of Plastic Extrusion in Modern Production
In the realm of modern production, the technique of plastic extrusion plays an important duty - plastic extrusion. This elaborate process, including the melting and shaping of plastic with specialized dies, is leveraged across different sectors for the creation of varied products. From car components to consumer items product packaging, the applications are large, and the potential for sustainability is equally outstanding. Untangling the principles of this procedure reveals the real versatility and capacity of plastic extrusion.
The Fundamentals of Plastic Extrusion Refine
While it may show up complicated, the fundamentals of the plastic extrusion process are based on relatively uncomplicated concepts. It is a manufacturing procedure where plastic is thawed and after that formed right into a continual profile through a die. The raw plastic product, commonly in the form of pellets, is fed into an extruder. Inside the extruder, the plastic undergoes heat and pressure, creating it to thaw. The liquified plastic is then compelled via a designed opening, referred to as a die, to create a long, continuous item. The extruded product is cooled down and after that reduced to the preferred size. The plastic extrusion process is thoroughly made use of in various sectors due to its versatility, cost-effectiveness, and performance.
Different Kinds Of Plastic Extrusion Strategies
Structure upon the standard understanding of the plastic extrusion procedure, it is required to check out the various strategies entailed in this manufacturing approach. In contrast, sheet extrusion develops big, level sheets of plastic, which are generally more processed right into products such as food packaging, shower drapes, and automobile components. Understanding these strategies is vital to utilizing plastic extrusion properly in modern manufacturing.

The Duty of Plastic Extrusion in the Automotive Market
A frustrating bulk of components in modern-day cars are products of the plastic extrusion process. Plastic extrusion important site is largely made use of in the production of different auto parts such as bumpers, grills, door panels, and dashboard trim. Therefore, plastic extrusion plays a pivotal role in auto manufacturing.
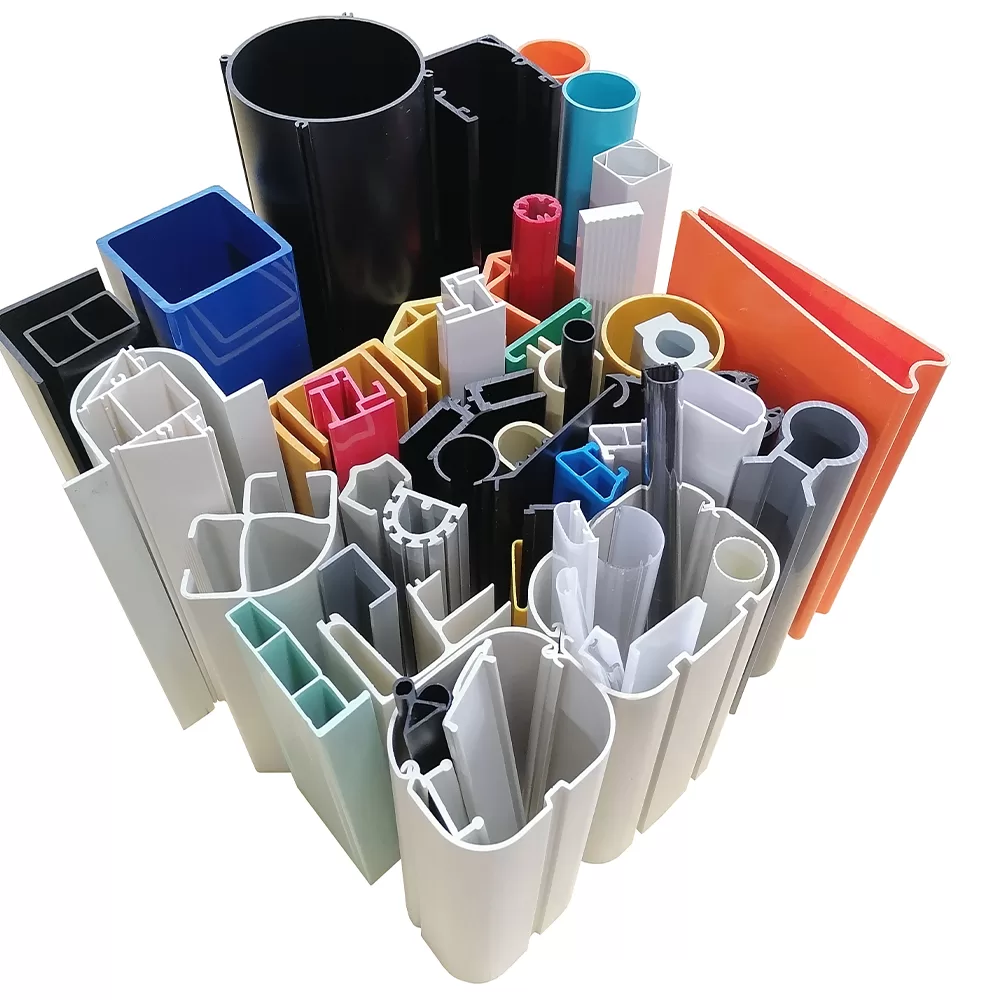
Applications of Plastic Extrusion in Consumer Item Manufacturing
Past its considerable effect on the automotive market, plastic extrusion confirms just as efficient in the world of customer items manufacturing. The adaptability of plastic extrusion enables producers to design and generate complicated forms and sizes with high accuracy and efficiency. The versatility, go now flexibility, and cost-effectiveness of plastic extrusion make it a favored selection for many consumer goods suppliers, contributing significantly to the market's development and development.
Ecological Effect and Sustainability in Plastic Extrusion
The pervasive usage of plastic extrusion in producing invites examination of its ecological ramifications. As a procedure that often utilizes non-biodegradable materials, the environmental impact can be significant. Power usage, waste manufacturing, and carbon exhausts are all concerns. Nevertheless, industry innovations are enhancing sustainability. Effective machinery reduces power use, while waste administration systems reuse scrap plastic, lowering basic material needs. In addition, the development of biodegradable plastics provides a much more eco-friendly alternative. In spite of these improvements, better technology is needed to alleviate the ecological footprint of plastic extrusion. As society leans in the direction of sustainability, manufacturers must adjust to remain sensible, emphasizing the significance of constant study and advancement in this area.
Verdict
In verdict, plastic extrusion plays an important function in modern manufacturing, particularly in the auto and customer goods industries. Comprehending the essentials of this process is vital to optimizing its advantages and applications.
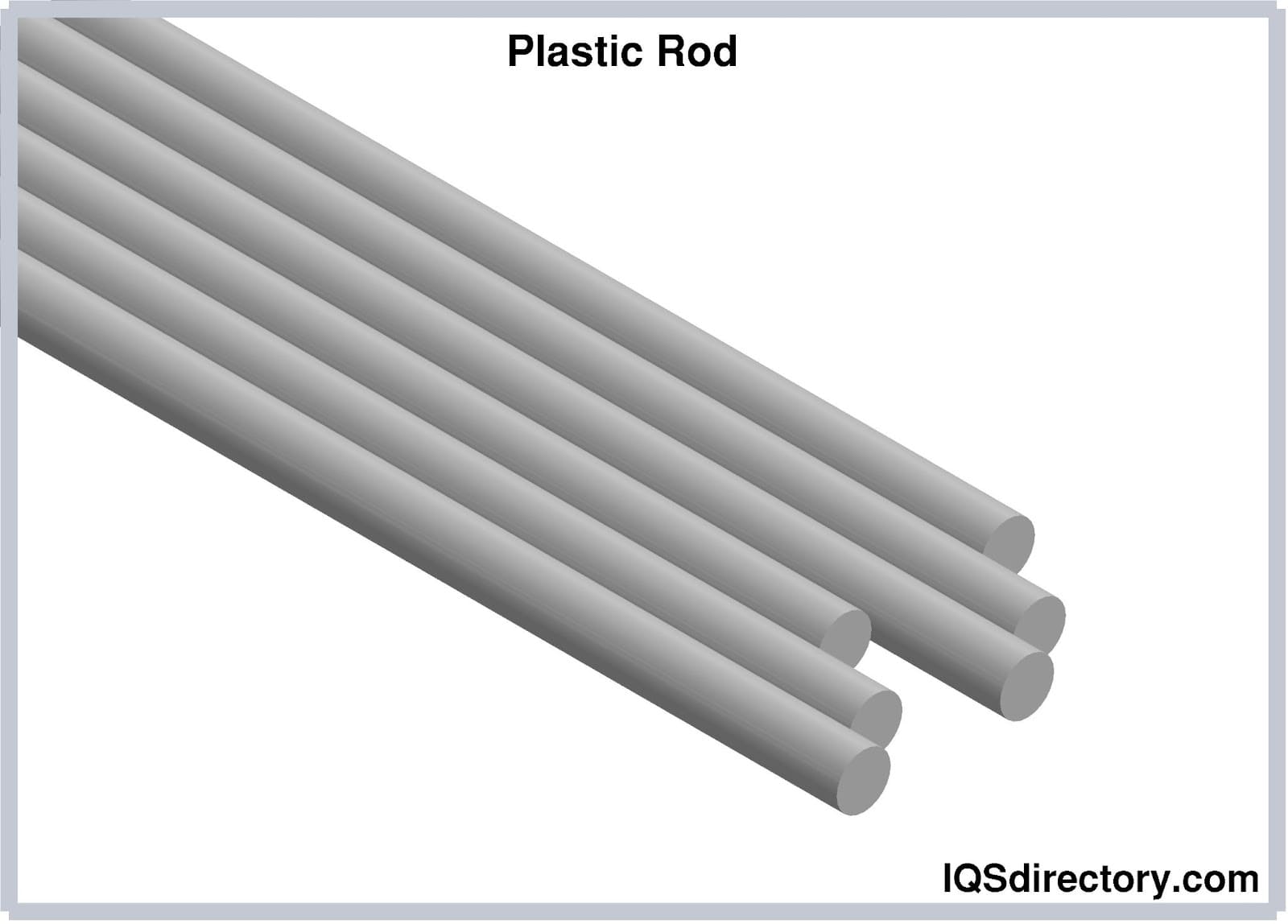
The official source plastic extrusion procedure is extensively used in numerous markets due to its effectiveness, cost-effectiveness, and flexibility.
Building upon the standard understanding of the plastic extrusion procedure, it is necessary to discover the numerous techniques involved in this manufacturing method. plastic extrusion. In comparison, sheet extrusion creates big, level sheets of plastic, which are typically more refined into products such as food product packaging, shower drapes, and auto parts.A frustrating bulk of parts in modern-day automobiles are products of the plastic extrusion process
Report this page